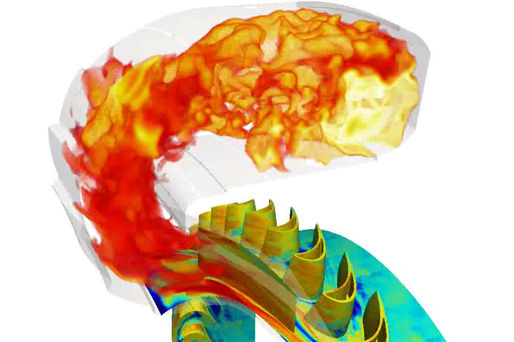
The « méthodes » group from TURBOMECA (led by L. Pons) and the CFD – combustion group from CERFACS (led by T. Poinsot) have recently actively collaborated to improve the design and life duration of helicopter engines.
Indeed in light of the ever increasing environmental constraints and current needs for ever more performant engines, being able to accurately predict the temperature levels entering the turbine stage becomes a key design constraint. Not only are the hot gas issued by the combustion process in the combustor still increasing, but their temperature now well overshoots the melting temperature withstood by existing materials of such engines. In an effort to improve the quality of the predictions issued by existing tools on this issue, CERFACS' team with the collaboration of the TURBOMECA team have supported multiple research projects (funded by RTRA, Europe…) to propose a CFD solution constructed around CERFACS' code that is AVBP.
From this active collaboration, recognized here by Teratec, has emerged a tool called TurboAVBP that can at once simulate the combustion chamber and the turbine stage thereby giving access to the entire spacial and temporal description of the flow field as well as its temperature level in the real engine geometry.
Constructed from the most advanced CFD research solutions, this tool hence allows to significantly improve the prediction quality of the next generation of engines at the design stage and provides a significant advantage to SAFRAN group in comparaison to its concurrents.
Link on l'Usine Digitale site : http://www.usine-digitale.fr/editorial/meilleure-collaboration-dans-la-simulation-numerique-cerfacs-et-turbomeca-calculent-simultanement-turbine-et-chambre-de-combustion.N336847
No content defined in the sidebar.